Our Process
Embark on a personalized design journey with us, starting from an initial consultation where we delve into your vision and aspiration for the project.
Our goal is to help bring your ideas to life, inspiring you with ideas along the way. Whether through site visits or video consultations, we look to understand the essence of your client's space and preferences.
Together, we’ll explore design and material options and feasibility, seeking input and feedback at every step. We then create an initial design rendering and work with you to refine dimensions and orientations before you sign off on the final design before fabrication.
Every step is tailored to individual preferences, making the process as unique as the end result. Our process is transparent, keeping you in the loop from start to finish.
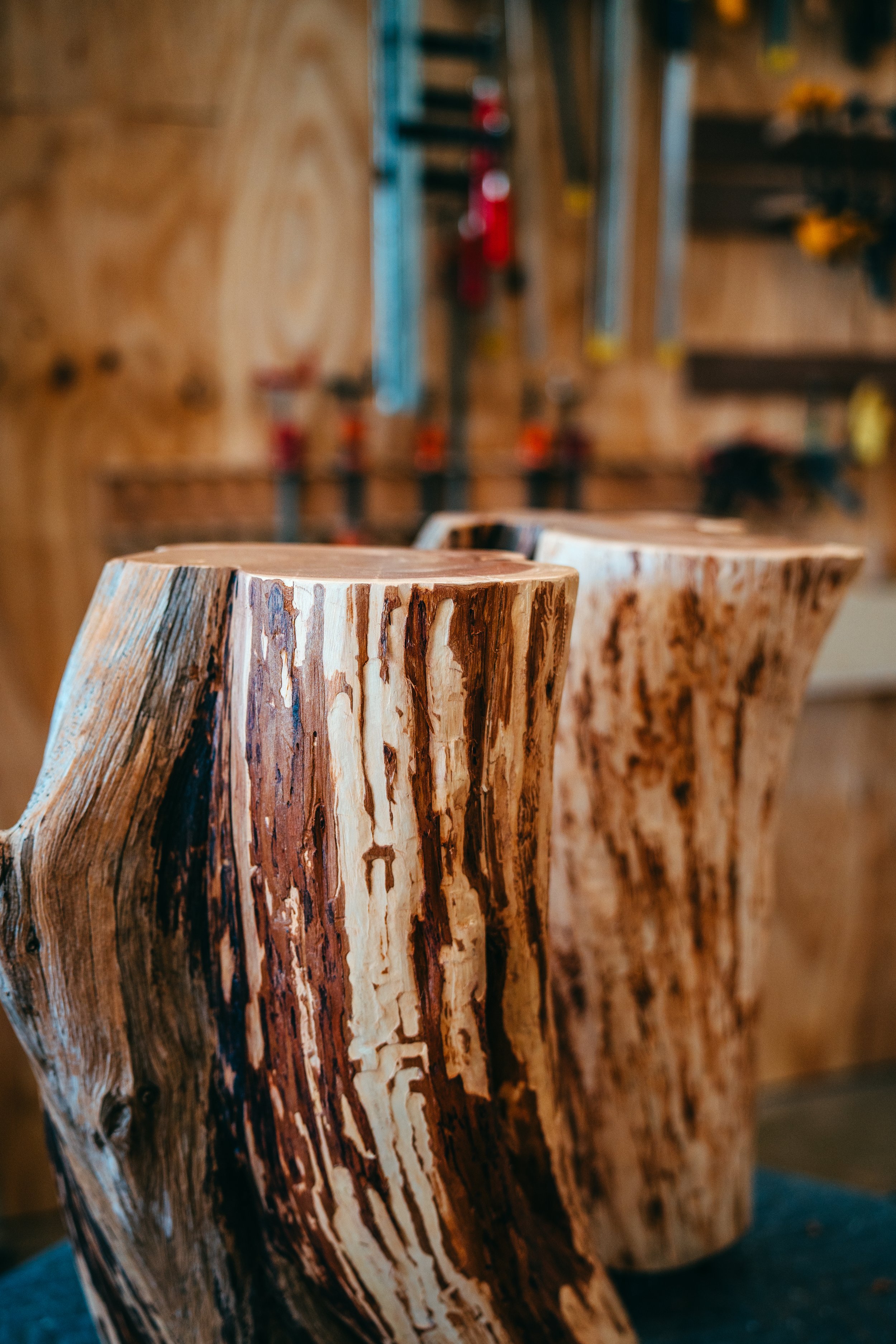
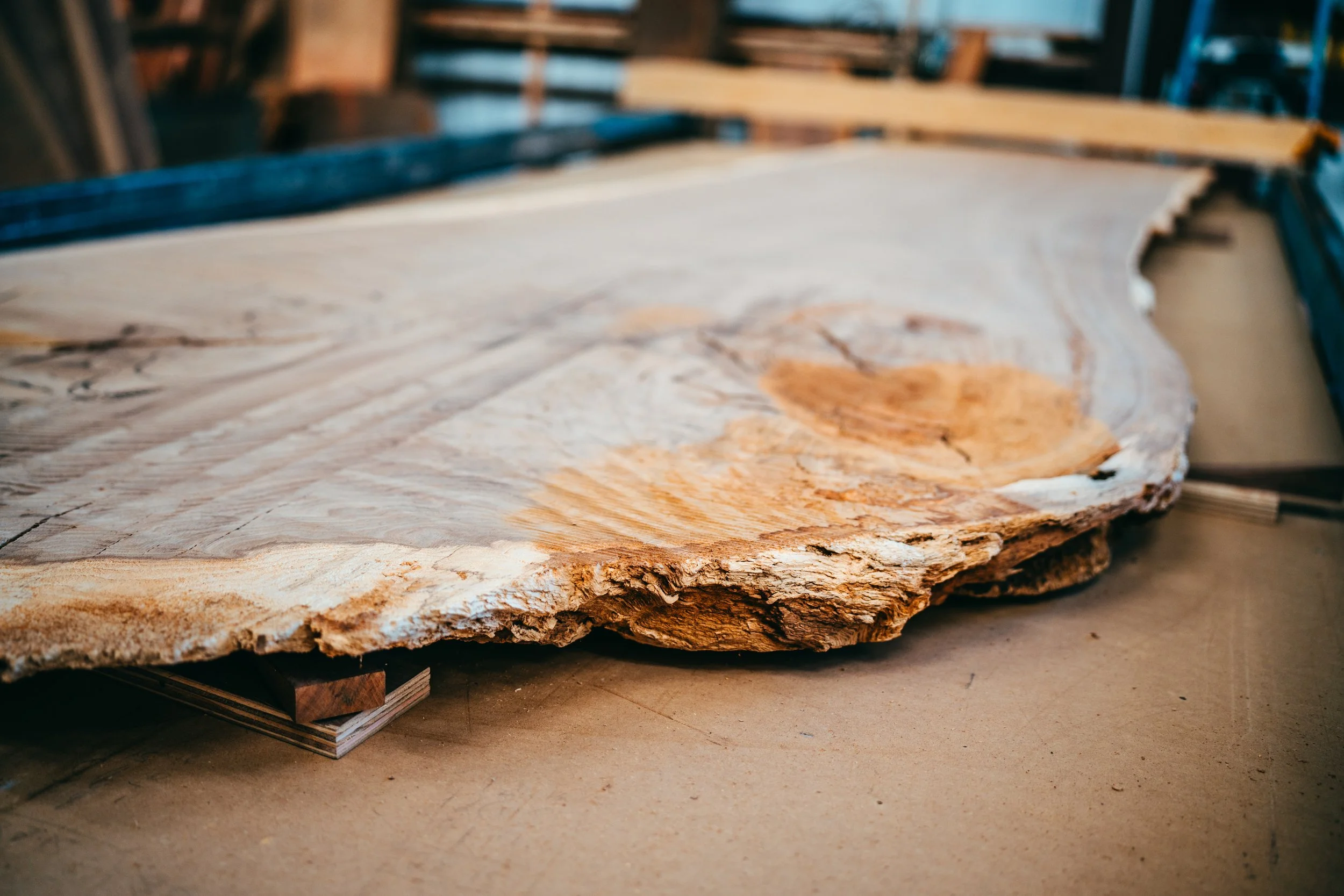
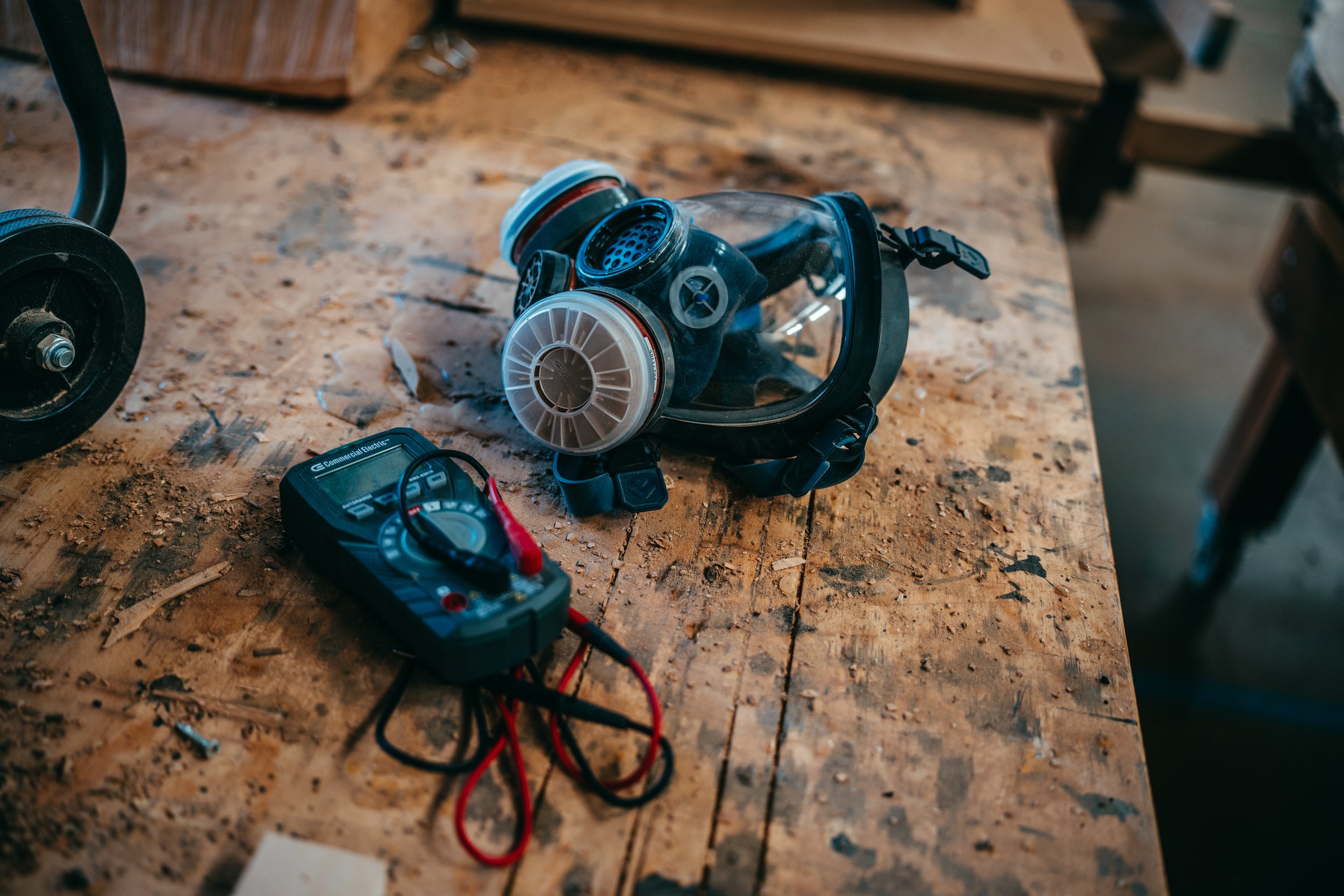
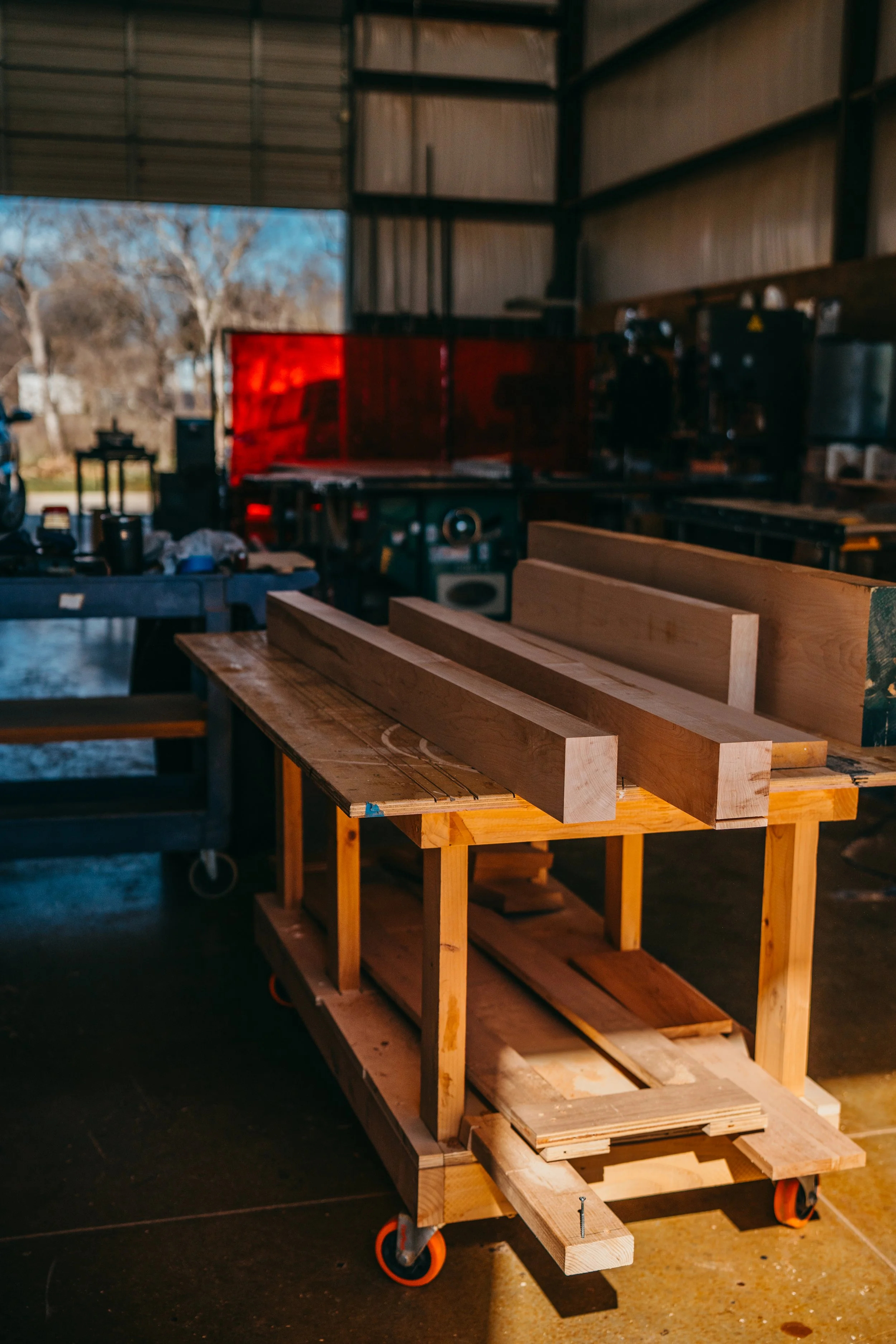
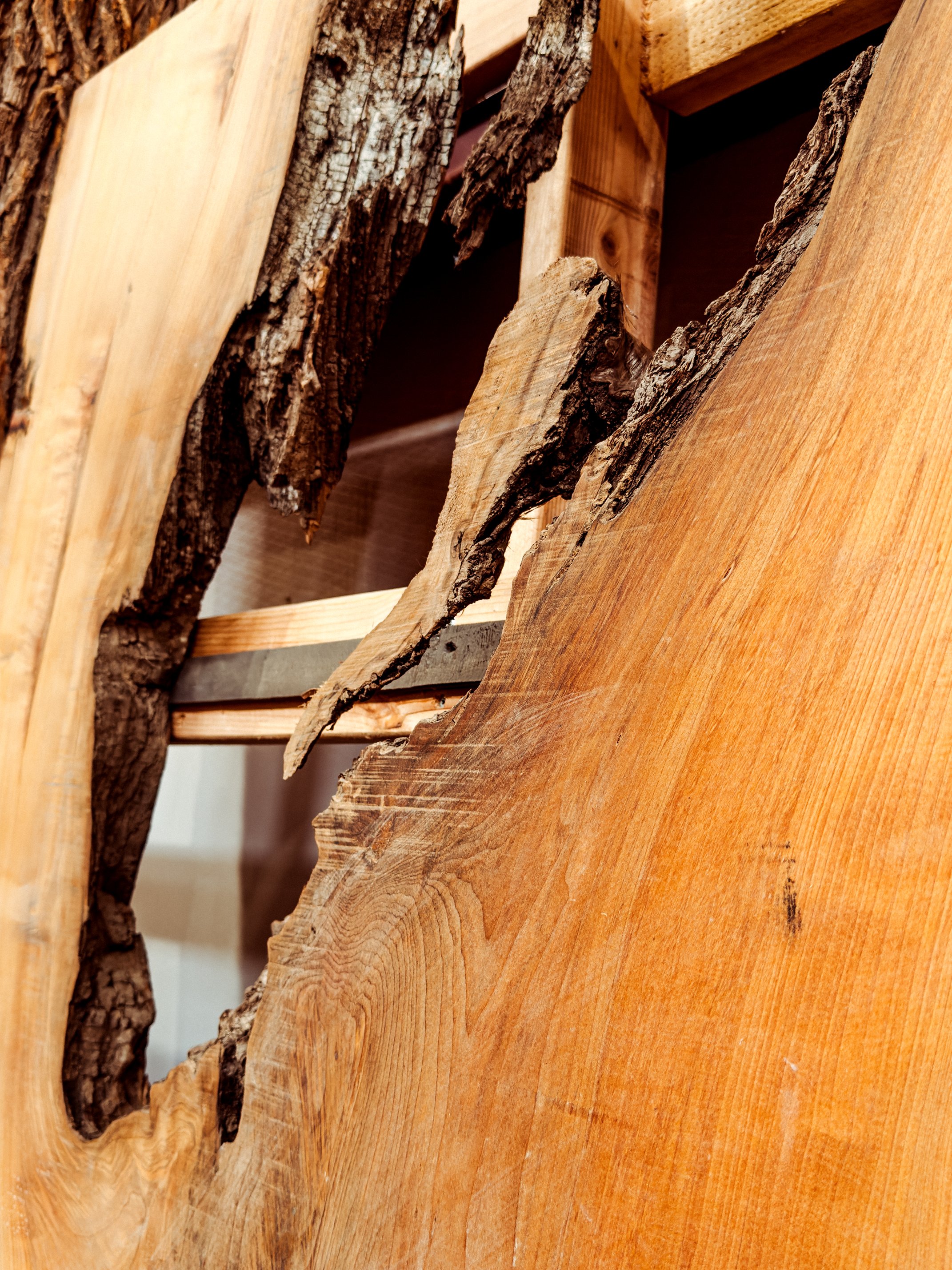
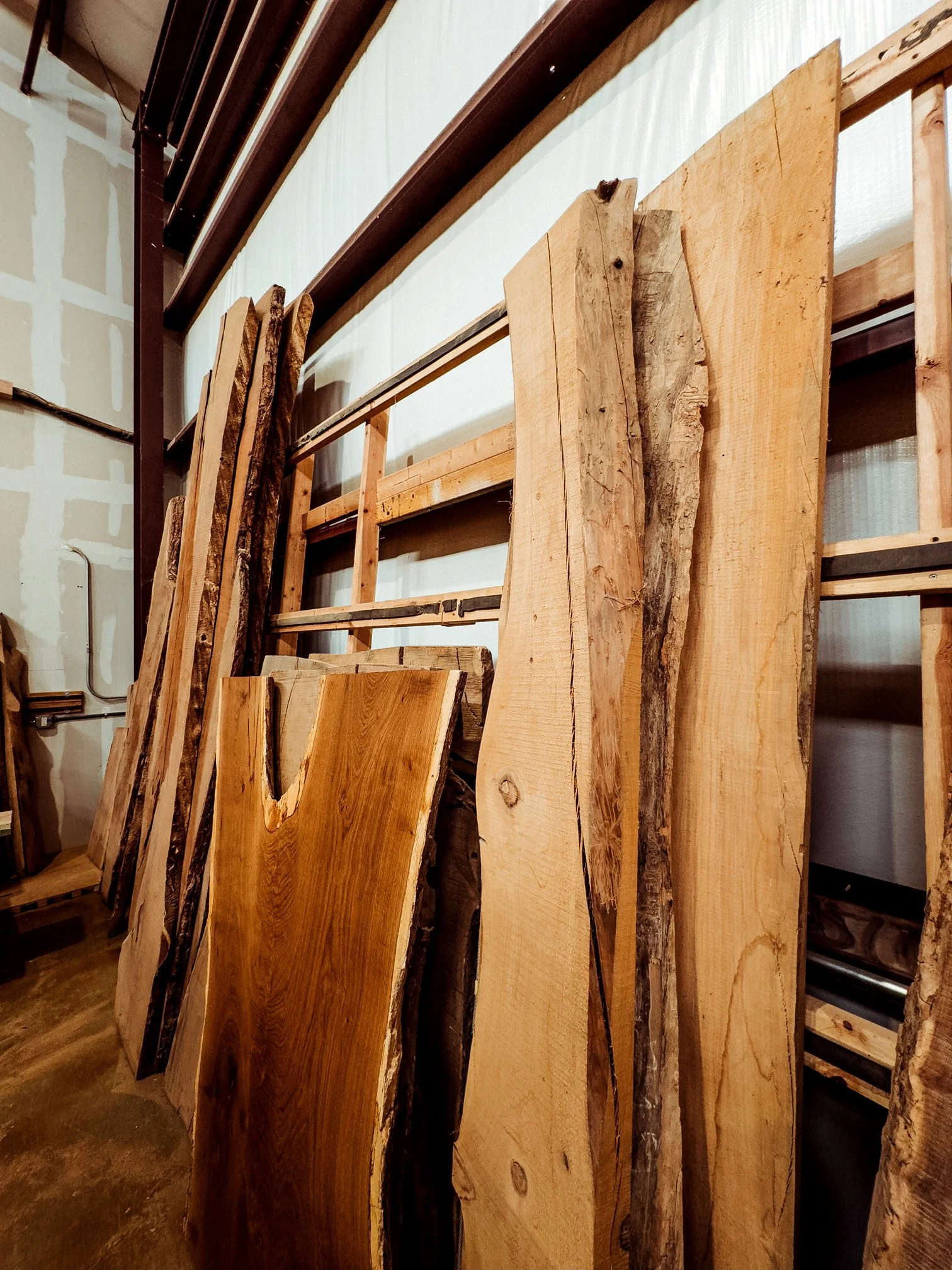
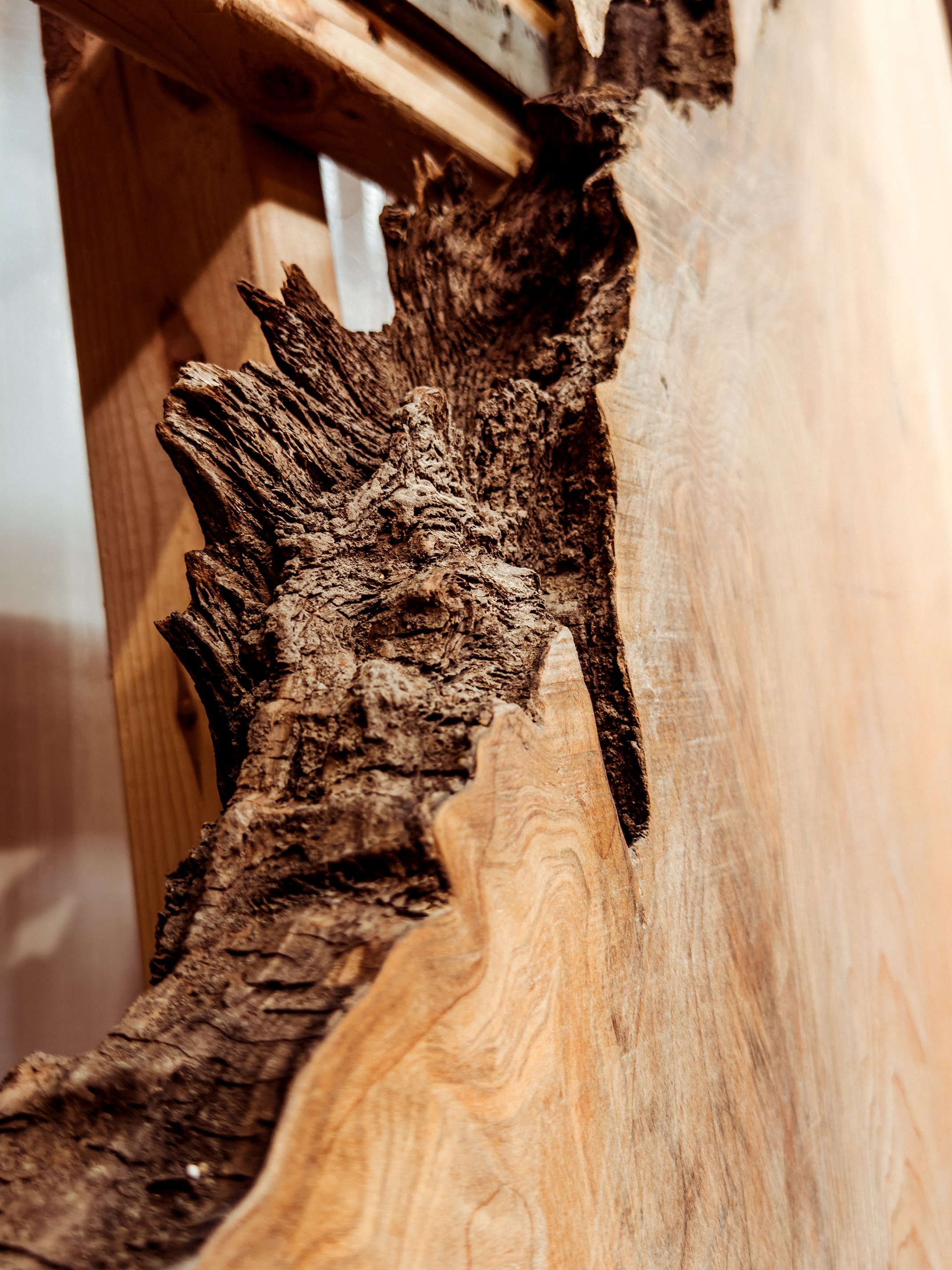
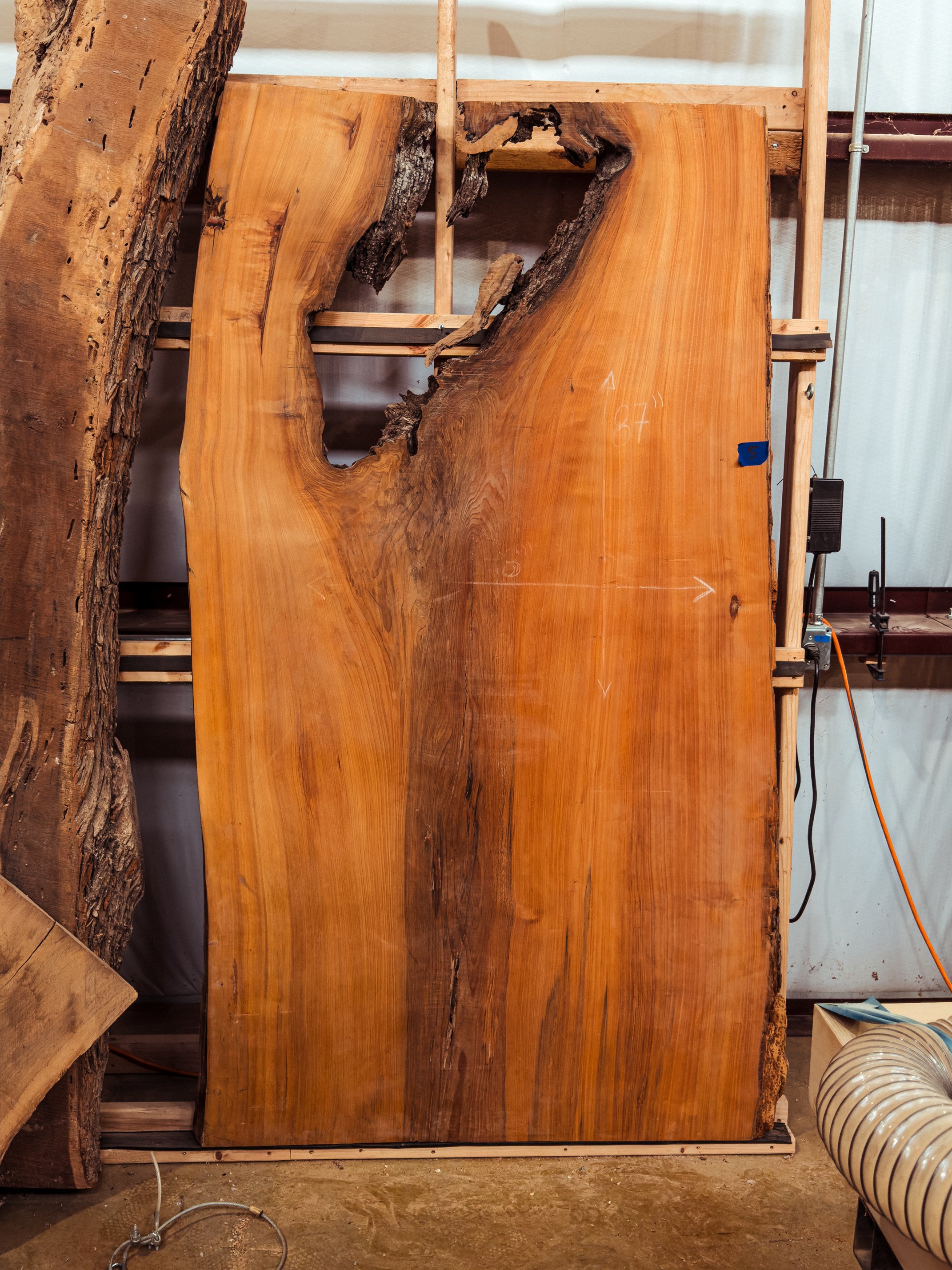
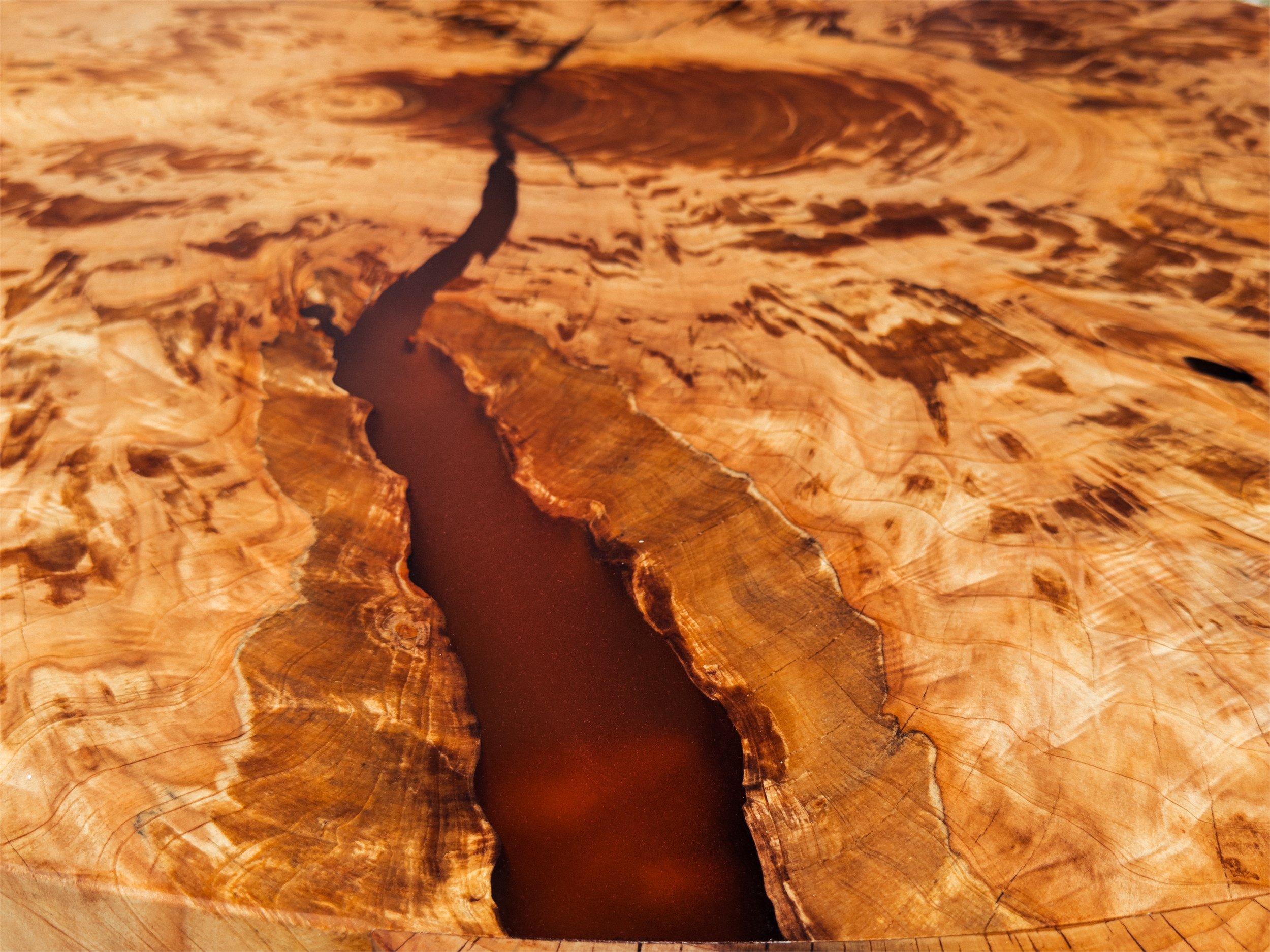
FAQs
What is the initial consultation process like?
At 4th Edition Design, we begin with a detailed initial consultation to understand your vision, needs, and preferences. During this meeting, we discuss:
Design Goals: We talk about your ideas, style preferences, and functional requirements.
Material Selection: We provide insights into suitable materials that match your aesthetic and durability needs.
Budget and Timeline: We outline the budget and timeline for the project to ensure it aligns with your expectations.
This consultation helps us gather all the necessary information to create a tailored design proposal.
How does the design phase work?
Once we have a clear understanding of your needs, our design team gets to work. The design phase includes:
Concept Development: We develop initial design concepts based on your input.
Sketches and Renderings: We create detailed sketches and 3D renderings to give you a visual representation of the final product.
Feedback and Revisions: We present the designs to you for feedback and make any necessary revisions to ensure the design meets your expectations.
This collaborative approach ensures that the final design reflects your vision and functional needs.
What happens during the material selection and prototyping stage?
After finalizing the design, we move on to selecting the best materials and creating prototypes. This stage involves:
Material Samples: We provide samples of different materials, finishes, and hardware options for your approval.
Prototyping: We create prototypes or mock-ups of key elements to ensure they meet the design specifications and functional requirements.
Approval: Once you approve the materials and prototypes, we proceed to the fabrication stage.
This process ensures that the final product is made with the highest quality materials and craftsmanship.
How does the fabrication process work?
Our skilled craftsmen bring the approved design to life through a meticulous fabrication process. This includes:
Cutting and Shaping: We cut and shape the materials according to the design specifications.
Assembly: The pieces are assembled with precision to ensure structural integrity and aesthetic appeal.
Finishing: We apply the chosen finishes, whether it’s staining, painting, or sealing, to enhance the beauty and durability of the piece.
Throughout the fabrication process, we maintain rigorous quality control to ensure the final product meets our high standards.
How is the delivery and installation handled?
Once the fabrication is complete, we coordinate the delivery and installation of your custom furniture. This involves:
Quality Inspection: A final quality inspection is conducted to ensure everything is perfect.
Delivery: We arrange for the safe delivery of your furniture to your location.
Installation: Our team handles the installation to ensure the piece fits perfectly in your space and functions as intended.
Follow-Up: We follow up with you to ensure you are completely satisfied with the final product.